The house
The pathway connecting the dwelling and jetty will be sandstone, which is found throughout the land already.
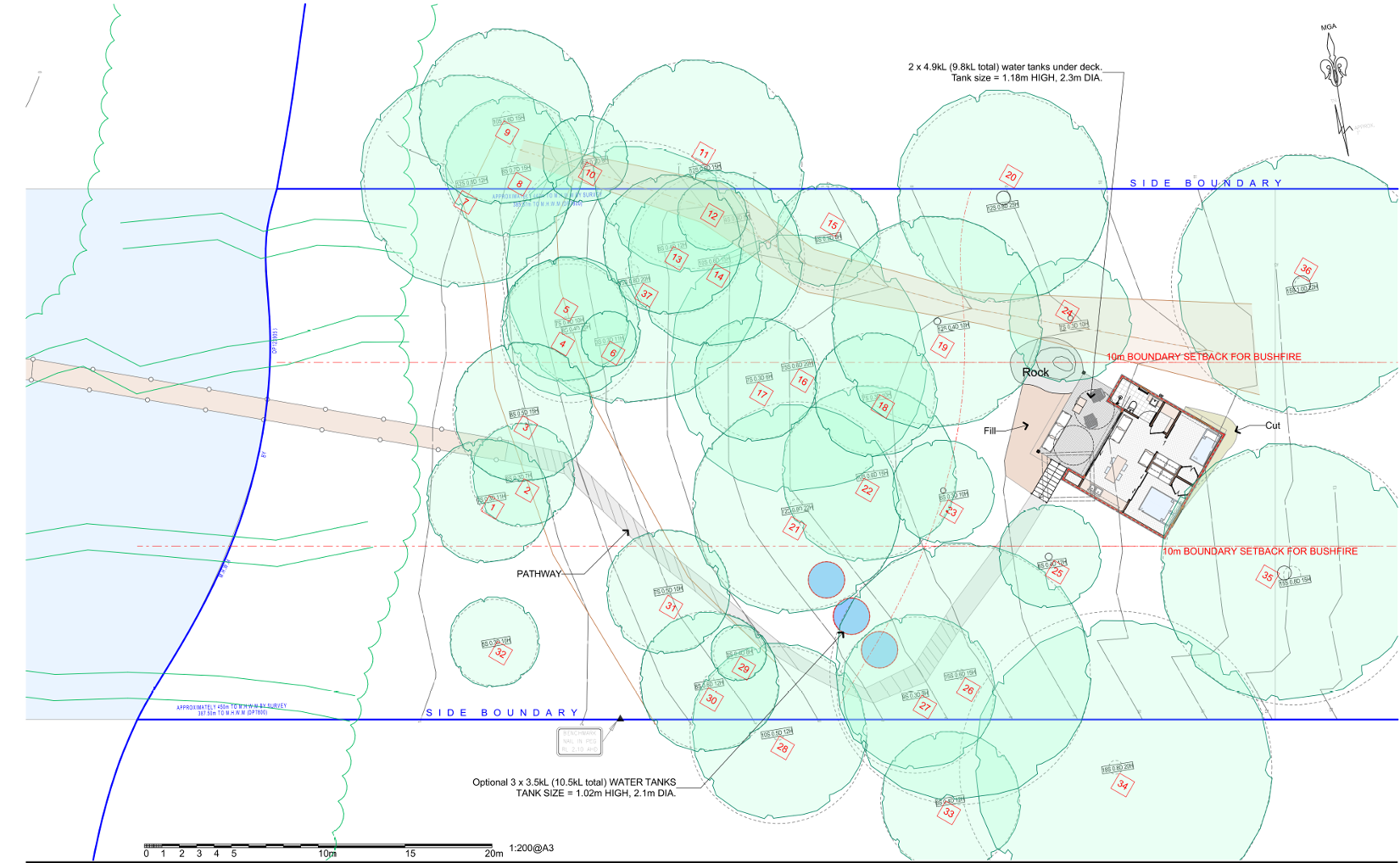
Setbacks and Topography
As can be seen from the site plan, the house component of the proposal includes significant setbacks from the Hawkesbury River, as well as the required 10m set-backs from each of the side boundaries (for asset protection zone requirements).
In response to the topography of the site, we hope to have the dwelling constructed on piers and to not need any significant earthworks and heavy equipment.
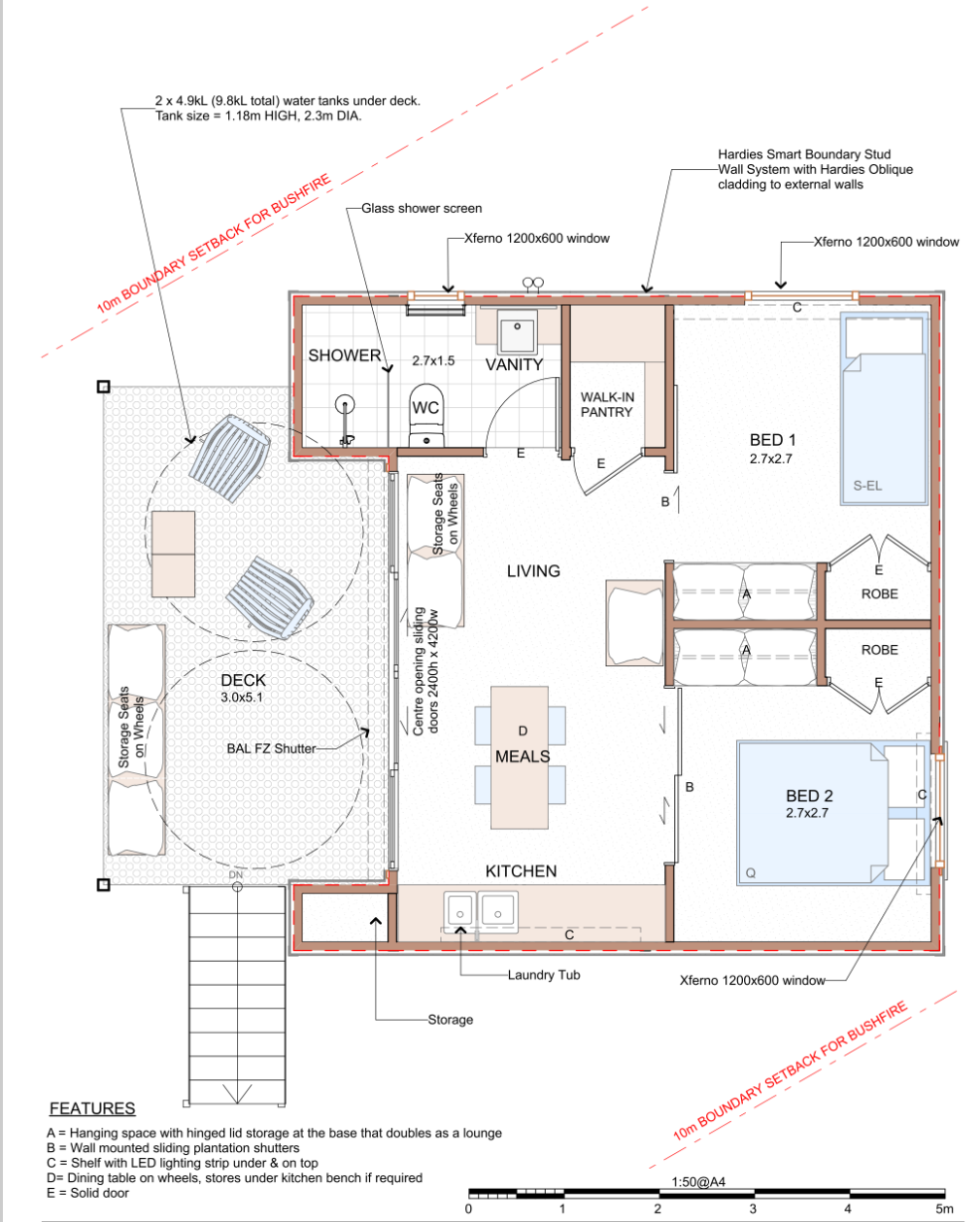
Minimizing Waste
We have designed the house to be very regular in shape, minimising the need for offcuts. We aim to have it so that the building materials will be able to be carried in by two men, thus decreasing the need for heavy machinery.
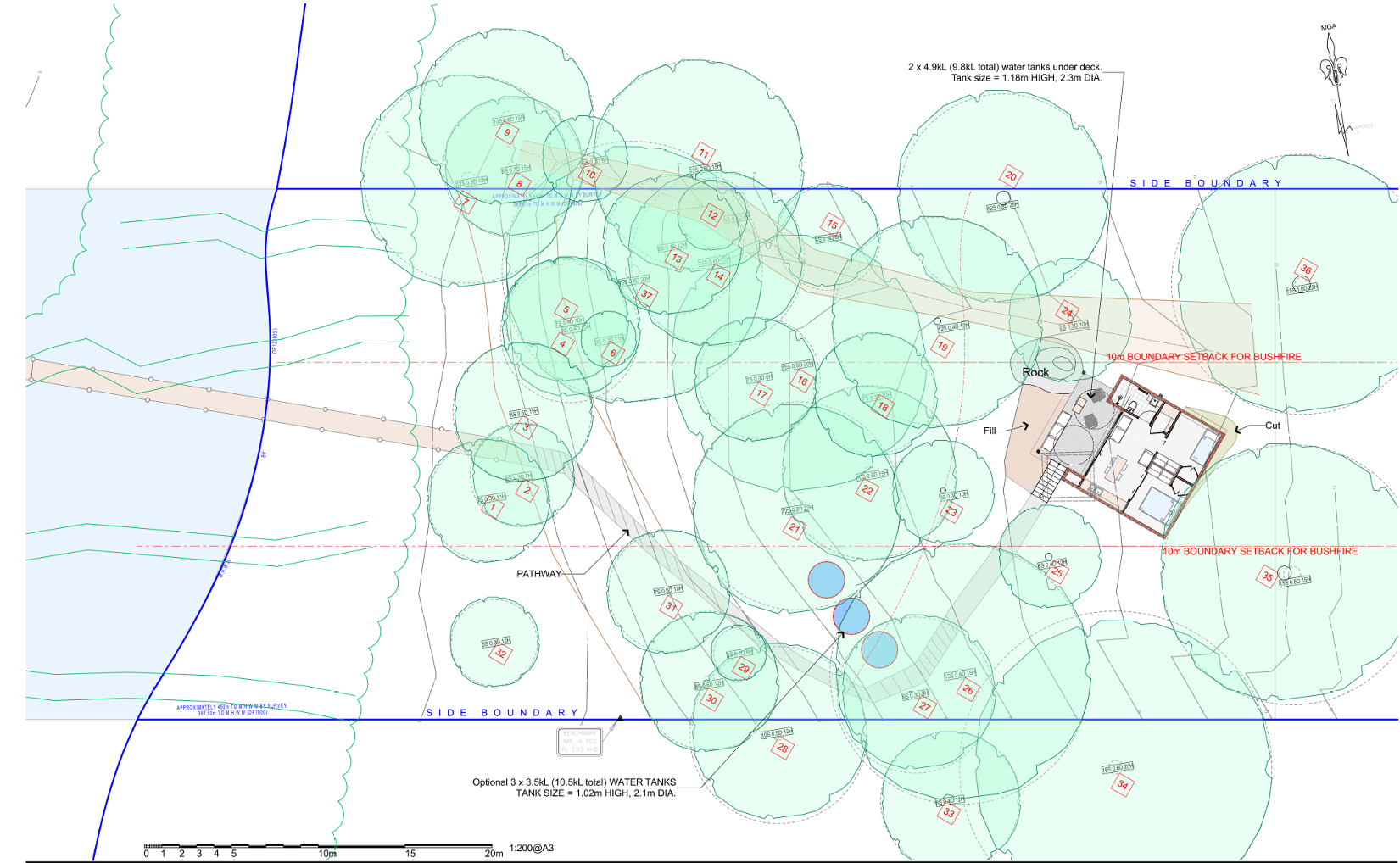
House size and Location
The size of the house has been chosen to minimise impact on soil and water flows as well as the visual impact and required level of clearing.
The location of the house was chosen in an attempt to maintain as much as possible the existing drainage paths and avoid altering natural water flow. This helps minimize erosion and preserves the natural hydrology of the area. In addition, the location was chosen to minimise required clearing to maintain the asset protection zone for bushfire protection.
We would like to hear your thoughts and suggestions.
Please don't hesitate to contact us with them!
Create Your Own Website With Webador